Phase transformation in materials and alloys
The role of stress and microstructure evolution during phase transformations in metals and alloys
Optimizing the properties of metals and alloys is generally achieved by exploiting phase transformations within the solid phase. The occurrence of such phase transformations is predicted thermodynamics and the rate by kinetics. Since phase transformations are associated by a volume change, also strains and consequently stresses are introduced in the materials. The stresses/strains at their turn affect the progress of the phase transformation. The most fundamental, and also the most complex, phase transformation in metals and alloys is known as martensitic transformation. This phase transformation is essential in the hardening of steels, but is also the basis for shape-memory alloys. Generally the transformation is considered infinitely rapid (instantaneous) and is therefore classified as athermal (independent of time). Recently it was recognized that martensitic transformations can be partly athermal, but have an important (sometimes dominant) time-dependent part. The extent of time-dependent vs. time-independent martensite formation depends on martensite’s internal structure. The ambitious goal in this WP is to following the phase transformation in-situ at sub-zero Celsius temperature and simultaneously visualize the development of the internal structure and the associated strains/stresses, with a combination of imaging and diffraction techniques. In parallel numerical simulation of the thermodynamics, kinetics and the role of stress is carried out. The importance in relation to 3D print is that these transformations should be understood and controlled, because the associated volume effects will be detrimental for near-net shape additive manufacturing.
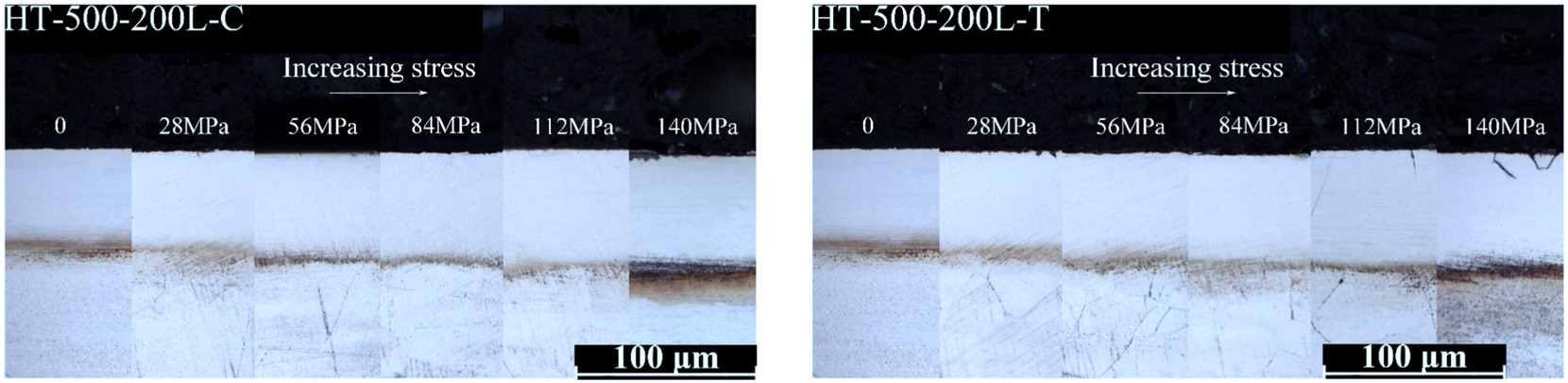